Modularly Optimised Production Processes
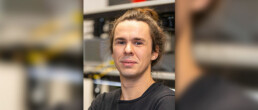
The Fraunhofer Institute for Material and Beam Technology IWS presented a system for AI-based optical surface and defects analysis in continuous production processes at Control 2024. This makes production faster, more accurate and more flexible. By combining artificial intelligence and optical measuring technology, defects are detected, classified, visualised and communicated to the production system in real time. The Control trade fair team spoke about the system with Dr.-Ing. Christopher Taudt, group leader for surface metrology at the Fraunhofer Institute for Material and Beam Technology IWS, Applications Centre for Optical Metrology and Surface Technologies.
Dr. Taudt, would you briefly explain what the SURFinpro system is?
Taudt: We’re specialised in surface assessment, in particular the detection of defects, surface roughness measurement and the identification of deviations. Our speciality is the integration of measuring technology into industrial systems. The measuring process takes place during the production process. Based on the example of a roll-to-roll process, we use our demonstrator for the SURFinpro measuring system to show how an optical scattered light method can be taken advantage of to reconstruct a surface in three dimensions and extract information about defects, scratches, inclusions, air bubbles and geometric deviations on the surface of the film, for example.
Which users are interested in this system?
Taudt: Users include manufacturers and processors of film materials. But other manufacturers are also interested, such as manufacturers of metal strips. The system isn’t just suitable for analysing the properties of products on rolls, but rather on sheet materials as well. We received corresponding enquiries at Control from potential customers who process sheet metal and bar stock.
How do projects and systems like this come about – does the industry approach you with specific tasks?
Taudt: In most cases the industry comes to us with a very specific problem and we take a detailed look at it. But of course we have a portfolio of our own measuring techniques that we can incorporate into this kind of process. Once our analysis has been completed, we decide which of our technologies – developed or refined by ourselves – are the best match.
What are the current topics in surface inspection – what’s the trend?
Taudt: It’s always interesting for companies to record as much information and as many measured values from the process as feasible, with the lowest possible investment. This might mean, for example, integrating several sensors into the system. Large measuring ranges, faster measuring processes and measuring procedures integrated into the manufacturing process are also important. From our point of view, automation and digitalisation play the most significant role. We’re moving away from stationary measuring instruments and quality testing in the laboratory, and towards direct integration into the manufacturing process in order to achieve continuous monitoring. Flexibility is also important, for example where materials and processes are concerned. It’s also necessary to capture as wide a range of parameters as possible.
Functions integration, flexibility and inline testing processes are thus the new benchmarks in quality control and quality assurance. How can you meet these challenges as a research institute?
Taudt: Customers turn to us as a research institute because they’re looking for a specific solution to their own respective problem. By the time a customer comes to us, he may have already approached several manufacturers of measuring systems directly, but hasn’t yet found the right answer as a standard solution. This is where we come into play as a research institute, because we’re the right partner for the development of application-orientated solutions.
In 2024, the Fraunhofer Institutes demonstrated their presence for the 18th time with the special show for “Contactless Measuring Technology” at Control.
Taudt: We attracted a specialised audience to our booth here in Stuttgart who can relate to the specific goals we cater to, and recognise the possible solutions. For example, in recent years we also exhibited hyper spectral imaging (HSI), a technology which is not yet available off the shelf. In the meantime, this division has been spun off from the institute and is now operating as an independent company, namely DIVE imaging systems.
How would you rate your contacts with expert visitors at this year’s Control?
Taudt: We’ve established highly specialised contacts at the event. The meetings have been top quality and the visitors are well informed, thus resulting in a very efficient and productive dialogue.